Grotnes’ Shrinker/Circumpress: Advancing Metalforming through Conveyor Roller Production
- Mike Walker
- Nov 14, 2023
- 3 min read
In the world of industrial machinery and conveyor systems, precision and efficiency are paramount. Grotnes, a pioneering force in metalforming technology, has been at the forefront of innovative solutions for more than 120 years.
One of our most widely applicable and standout creations is the 12-HS-175-8 175-ton shrinker, a versatile machine with the ability to easily produce conveyor rollers, including drive pulleys and idler rollers. The shrinker/circumpress is often employed in the production of rollers for use in automotive plants, distribution centers, logistics warehouses and other commercial environments.
In this blog post, we’ll look closely at the shrinker/circumpress, detailing its capabilities and operational benefits.
Grotnes Shrinker/Circumpress: An Overview
Our shrinker/circumpress is a cutting-edge machine designed to easily shape tubes, forming diverse sizes of tapered rollers, including full taper, fast taper with crown, negative crown and other shape variations.

The shrinking operation works in direct contrast to expansion processes.
The component is positioned within the shrinker, presenting its external diameter to the shrinker’s tooling. The dies then exert inward pressure, manipulating the metal component past its yield threshold to achieve the requisite shape and dimensions. What makes it particularly attractive for the manufacturing of conveyor rollers is its exceptional adaptability and simplified process to form rollers from standard tubing.
Let’s delve into the shrinker’s key features and additional benefits.

1. Safety Measures: Safety is top of mind in any industrial setting, and Grotnes is committed to protecting those who use our products. Our shrinker/circumpress includes a light curtain and necessary interlocks to enhance the operator's safety in the forming process.
2. Quick-Change Tooling for Customization: The shrinker comes equipped with easily interchangeable tooling, allowing for the creation of rollers with different diameters and taper angles.
3. User-Friendly Controller: Grotnes recognizes the importance of ease of operation. Our shrinker/circumpress is fitted with a user-friendly, recipe-driven controller, making it straightforward to setup and transition between different roller sizes. This feature helps to streamline the production process, reducing downtime and increasing productivity.
4. Rapid Production: The shrinker/circumpress can form a conveyor roller in less than 60 seconds, allowing for high-speed production and expedited order fulfillment. Traditional, antiquated methods of forming rollers often involved extensive machining, contouring and welding in fixtures.
5. Exceptional Precision: Our machine ensures the rollers produced exhibit exceptional concentricity and size accuracy, typically within .005 or better. The machine also features a loading table that supports the pipe on the center line as it undergoes the forming process. This precision makes certain the final product meets stringent quality standards and performs optimally in conveyor systems.
6. Simplified Bearing Assembly: The shrinker/circumpress offers the ability to size the conveyor roller ends and form location ridges, simplifying the correct assembly of bearings. This further streamlines the manufacturing process and reduces the chances of errors in assembly.
7. Versatility: Perhaps of the most compelling advantages of the shrinker/circumpress is its versatility. It can be configured to form a wide range of sizes and shapes, making it an inherent all-in-one solution for conveyor roller production.
How Grotnes Can Help
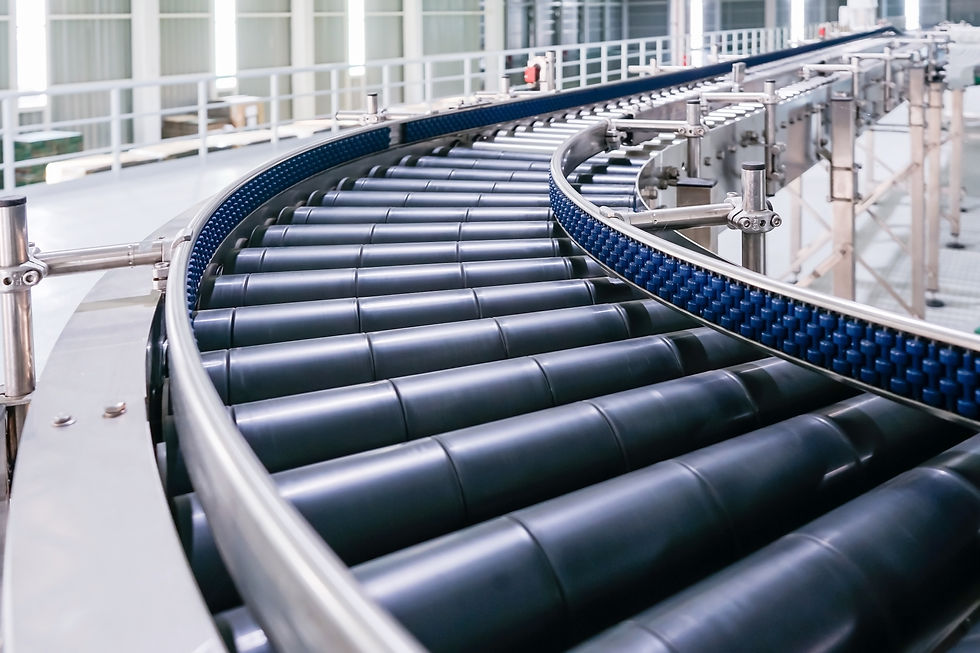
Grotnes’ shrinker/circumpress represents a significant advancement in the production of conveyor rollers and various other applications. Its adaptability, efficiency and precision make it an indispensable tool for industries that rely on manufacturing these critical components. Our shrinker/circumpress technology can be used in several applications within different industries, capable of forming not only tubes but rings and hoops for applications such as pipe couplings, jet engine parts, catalytic convertors and many others.
At Grotnes, our experienced staff is always ready to assist and guide you in harnessing the full potential of our shrinker/circumpress. Give us a call with your vision today, and one of our team members can share how we can help!
Comments