When forming the end diameter transition for exhaust components such as catalytic converters or resonators, tube spinning stands out as a highly cost-effective solution for manufacturers. At Grotnes, our advanced spinning technology excels in this application and others, offering versatile solutions for creating concentric, eccentric and oblique shapes through our vertical spinners, concentric spinners and EST-OST spinners.
Our machines’ spinning applications are vast and versatile, including but not limited to:
Catalytic converters and mufflers/resonators
Couplings for bulk transfer
Components for motorcycle suspension
Housing for fuel cells and filtration systems
Sanitary floor drains tailored for the food industry
Preforms designed for hydroforming
Various couplings and reducers
Fuel filler tubes
Airbag inflator cylinders
The Power of Spinforming Technology
Spinforming technology eliminates the need for welded tube end-pieces, enhancing the overall quality and reliability of components. Compared to other manufacturing processes, spinning is often more efficient and can integrate with cast, drawn, forged or machined parts to reduce costs and boost production.
Concentric Spinners
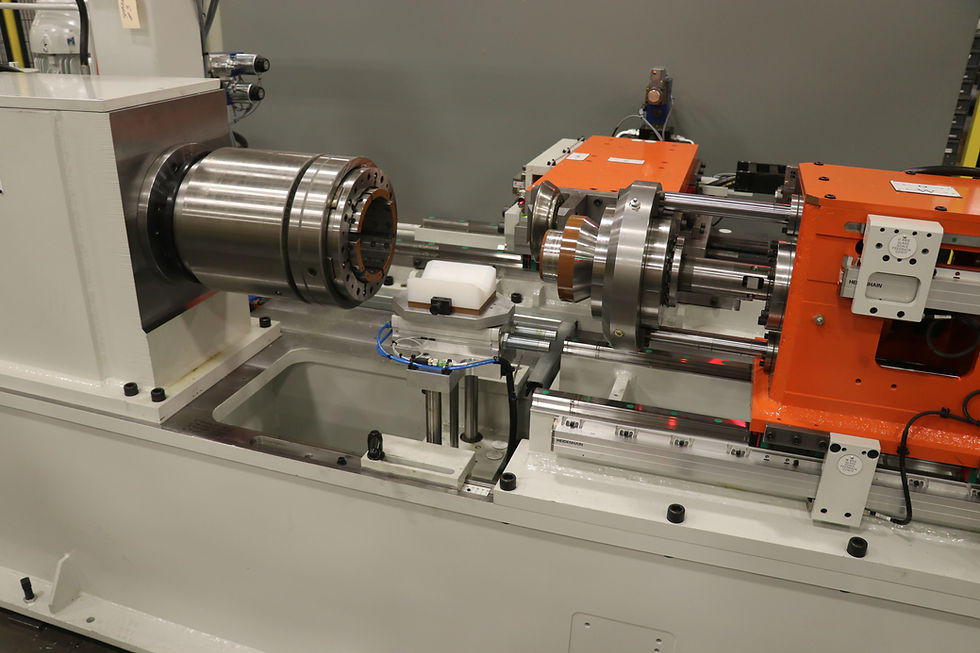
Our concentric spinning machines are ideal for a variety of industries, including automotive, consumer products, general industrial, lighting and military applications. These machines produce chipless formed parts with repeatable and precise CNC controls, accommodating materials such as steel, stainless steel, aluminum, copper, brass and exotic alloys. Grotnes concentric spinners range from simple, manually operated machines to fully integrated, automated manufacturing cells and high-volume production lines.
Key features include:
Multiple spinforming machines for parallel production
Flexible cell concepts
Automatic material handling system options (robots, conveyors, hard automation)
CNC process control
Real-time split tube detection
Automatic slide lubrication
Flexible collet-style chuck
Quick-change tooling
Net shape length control
Compact footprint
Vision system check station
Laser diameter verification
For catalytic converters, concentric spinners can be equipped with a shrink assembly sizing system, converter element inspect/reject station and automatic inner cone insert/spin system.
EST-OST Spinners
Grotnes’ EST-OST spinners are used for end forming cylinders or tubes, featuring a unique process where a clamped workpiece and rotating head with forming rolls work in unison. This technology allows for the formation of a reduced end profile that is offset or eccentric from the tube’s central axis by moving the clamped workpiece toward the offset axis while the forming rolls reduce the diameter.
Similarly, an oblique end profile is achieved by driving the clamped workpiece and moving the forming rolls radially toward the oblique axis. Ideal for automotive or truck exhaust components and catalytic converters, this EST-OST spinner technology offers a 30% reduction in manufacturing costs and process energy compared to alternatives, improved quality through reduced welding and flexible tooling design.
Vertical Spinners
Our vertical spinforming machine is designed to be a standalone powerhouse in your production line. It can easily integrate into a small cell of machines for a more comprehensive manufacturing process, including trimming, leak testing and part handling. The complementary processes are controlled independently but can be synchronized for maximum efficiency.
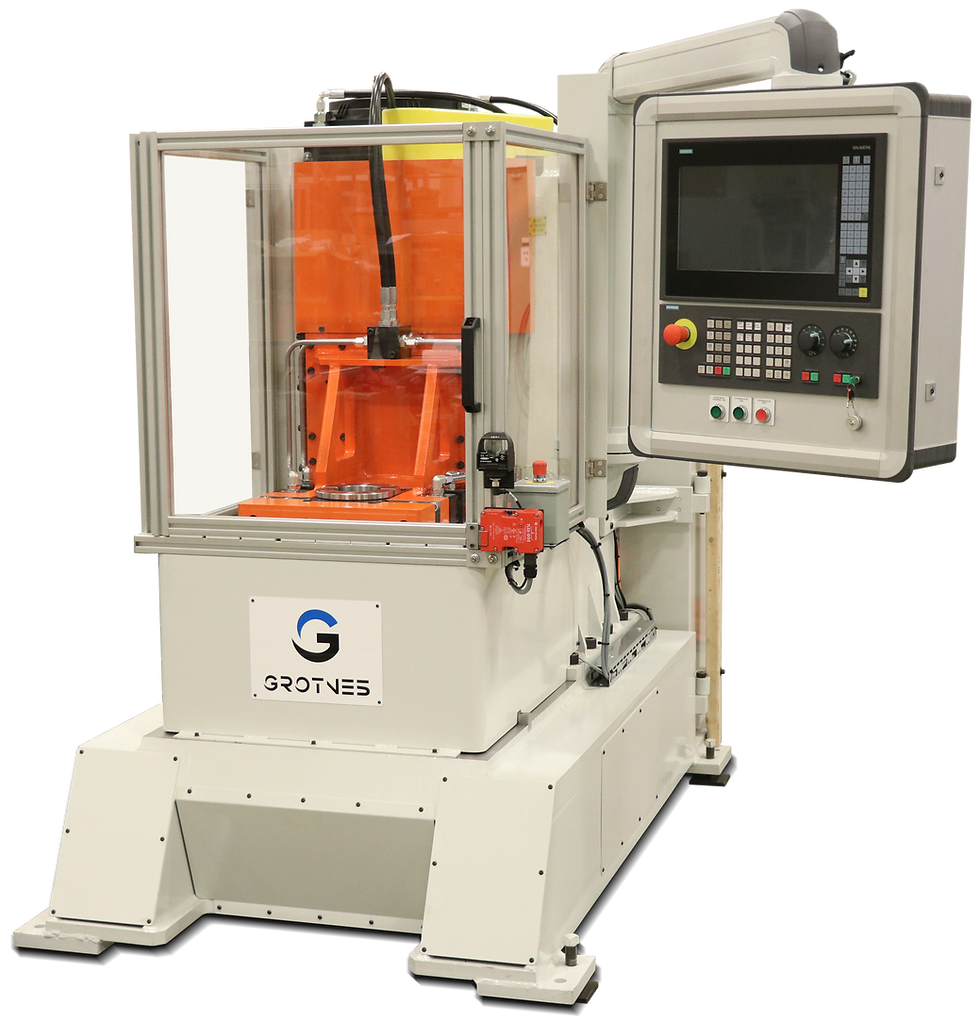
Benefits of the Vertical Spinner
Compact Footprint: Less than 3 square meters, making it ideal for limited spaces.
Efficient Layout: Width of approximately 1 meter for close proximity of adjacent equipment.
Ergonomic Load Height: Less than 1000 mm for comfortable handling.
High Performance: Spindle speed up to 1000 RPM with rugged stiffness and high bearing life.
Speed and Efficiency: High-speed slide velocities reduce cycle time, with typical cycles forming one end in just 40 seconds.
Versatile Tooling Options: Internal mandrel tooling and Siemens controls allow for flexible and precise operations.
Integration Ready: Can be combined into manual or robot-loaded cells for enhanced automation.
Size and Thickness Capacity: Accommodates part diameters from 54 to 177.8 mm (2.12 to 7.00 inches) and a wall thickness of up to 2.0 mm (0.079 inches).
Key Savings of Spinforming
Grotnes’ spinforming technology offers significant savings and productivity enhancements for a variety of manufacturing applications.
Reduced Inventory: Simplifies stock management and decreases storage costs.
Reduced Assembly: Minimizes the need for assembling multiple component parts.
Reduced Tooling: Cuts down on time and manpower required for extensive tooling setups.
Advantages of Spinning
Our spinning machines are designed to enhance your manufacturing process with superior quality and efficiency.
Eliminates Welding Process for End Cones: No need for welding, which can potentially introduce weak points to your components.
Eliminates Leaks from Weld Processes: Ensures a sturdier and more leak-proof product.
Eliminates Weld Gases/Indoor Pollution: Promotes a healthier work environment.
Process Flexibility: Can replace expensive end cone tolling with versatile spinforming techniques.
Shortens Product Development and Design Changes: Facilitates quicker adaptations and iterations.
Different Angles Possible: Allows for the creation of eccentric and oblique ends.
Length Control: Optional feature for precise product specifications.
Eliminates Trim Equipment: Reduces the need for additional trimming machinery.
Lowers Material Cost: No trimming scrap results in material savings.
Vertical Design: Efficient use of shop floor space with concentric spinning options.
Why Choose Grotnes?
At Grotnes, we pride ourselves on our extensive process knowledge and commitment to innovation. Our laboratory and prototyping equipment, available through our prototype initiative Formitt Metal Labs, allow us to develop custom parts based on your distinct manufacturing challenges. We offer high levels of maintainability, reliability and consistency in our machines, ensuring your production operates smoothly and efficiently.
Our worldwide service and sales network ensures you receive local support whenever and wherever you need it. Contact the Grotnes team today to learn more about our comprehensive suite of metalforming solutions!
Comments