At Grotnes, precision and innovation in metal forming are our day-to-day reality, brought to life by our prototype initiative, Formitt Metal Labs.
Through a synthesis of advanced machining and engineering, we excel in co-manufacturing bespoke, hollow tube shapes and components. Our expertise spans across essential components such as exhaust catalytic converters, offering cost-effective and quality-driven solutions. But Formitt Metal Labs’ contribution doesn’t stop at prototyping. With more than 120 years of industry expertise, we’re pioneers in process innovation, focused on reducing waste and enhancing efficiency. Our development and production services cater to diverse sectors, from automotive to marine exhaust components, ensuring each client receives tailored solutions.
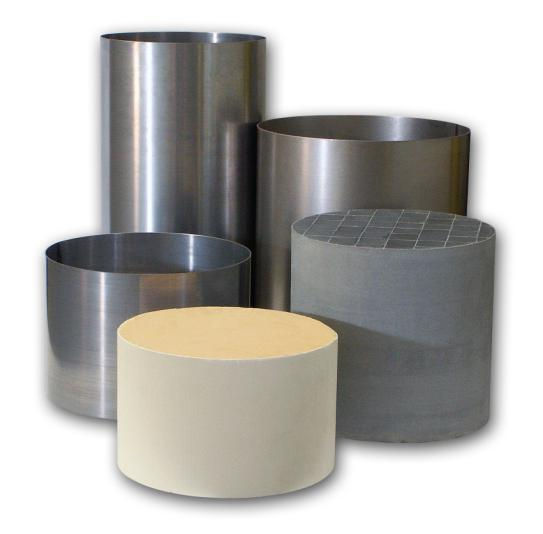
Leveraging the advanced capabilities of Grotnes machines, Formitt Metal Labs provides smaller production runs that cater to the initial stages of product development. This approach is particularly beneficial for customers who are in the process of scaling up their operations. Initially, when the production requirements are modest, our clients can rely on Formitt for high-quality, custom-made components. As their production needs grow and they approach a scale where owning a Grotnes machine becomes essential, we ensure a seamless transition. This flexibility not only helps in maintaining quality during the critical phase of product growth but also provides a cost-effective solution for our customers during their journey from prototyping to large-scale production.
Our North American facility is rare in its capability to fully develop on-site processes, a feature that allows us to deeply understand and meet your long-term production needs. Whether the task is to manufacture components or assist in transitioning to independent machine operation, Formitt Metal Labs is committed to ensuring a smooth path for our partners.
Formitt Metal Labs’ Services
The Formitt Metal Labs facility is a hub of innovation, where our specialists harness advanced techniques to produce parts for durability and market testing. Our comprehensive services include:
Part and tooling development
Assessing material suitability
Process feasibility studies
Productivity assessments
Full-scale production runs
Lab Equipment Capability
Metal Formitt Labs prides itself on comprehensive in-house design, engineering and production capabilities:
Spinning equipment with concentric, eccentric and oblique spinning technologies.
Round or oval canning equipment, featuring barrel sizers, programmable stuffers, patented AGC (Adaptive Gap Control) and pressure-monitored testing systems.
Spinning Technology
Spinning technology is a cornerstone of our manufacturing prowess. It’s a cost-effective approach for producing high-caliber, seamless cylindrical parts and assemblies. Adopting spin-forming technology results in significant savings by reducing the need for inventory, assembly, tooling and welding, streamlining the manufacturing process.
Our spinning applications are vast and versatile, including but not limited to:
Catalytic converters and mufflers/resonators
Couplings for bulk transfer
Components for motorcycle suspension
Housing for fuel cells and filtration systems
Sanitary floor drains tailored for the food industry
Preforms designed for hydroforming
Various couplings and reducers
Fuel filler tubes
Airbag inflator cylinders
Canning Technology
Our canning technology is at the forefront of assembling catalytic converter substrates with support mats into stainless-steel tubes, ensuring durability and performance.
Other Capabilities:
Shrinking
Expanding
Roll Forming
Fulfill Your Vision with Formitt Metal Labs
We invite potential customers to witness the Formitt Metal Labs difference. Our team is ready to guide you through the process of metal forming, offering personalized consultation to address your distinct manufacturing challenges.
Connect with Grotnes and Formitt Metal Labs today to experience a partnership that not only meets but anticipates and innovates upon your production needs.
Comments